The acoustical design for The Kendeda Building included: exterior noise control, mechanical systems noise control, sound isolation, impact isolation, and reverberation control. In addition, we had to adhere to the LBC and identify acoustical products that do not contain Red List materials or chemicals (777 in total) that have the greatest impact to human and ecosystem health. In other words, not only did we optimize acoustical performance, we did so while taking into account occupant health.
The acoustical team chose to base the design goals on ANSI/ASA S12.60/Part 1 American National Standard Acoustic Performance Criteria, Design Requirements, and Guidelines for Schools, Part 1: Permanent Schools. The Petals of the Living Building Challenge do not currently include acoustical design concepts, but it is our hope that future iterations will include acoustical design as a component.
One of our proudest achievements is moving the acoustical manufacturing industry further along in considering sustainable options for acoustical products. Prior to this project, very few acoustical options were available on the ILFI Declare system or noted by they manufacturers as Red List free. Our investigations brought the Red List to the attention of acoustical manufacturers and now there are more documented sustainable acoustical products readily available. The products selected for this project, specifically the mineral wool, met many of the project guidelines in addition to acoustics. This is discussed further in the Reverberation Time section.
Prior to the construction of the Kendeda Building, professors working in and around the project site expressed daily discomfort due to the mechanical system noise coming from adjacent buildings. Elimination of that noise has lead directly to improvements in their and others' lives. The noise investigation and mitigation is outlined in the Environmental Noise section below.
We are pleased to report that the users are happy with the acoustical atmosphere in the building. The following narrative outlines some of the specific challenges and acoustical opportunities in the building but are not an exhaustive listing of all aspects of the acoustical consulting on the project.
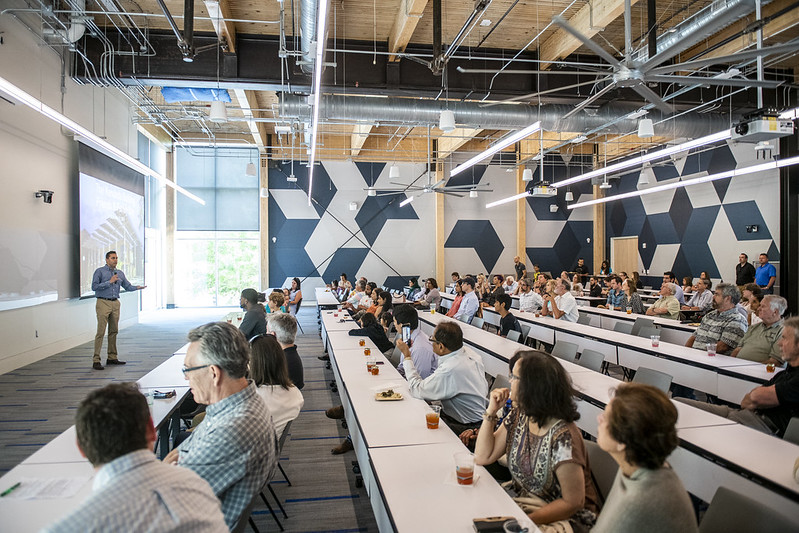
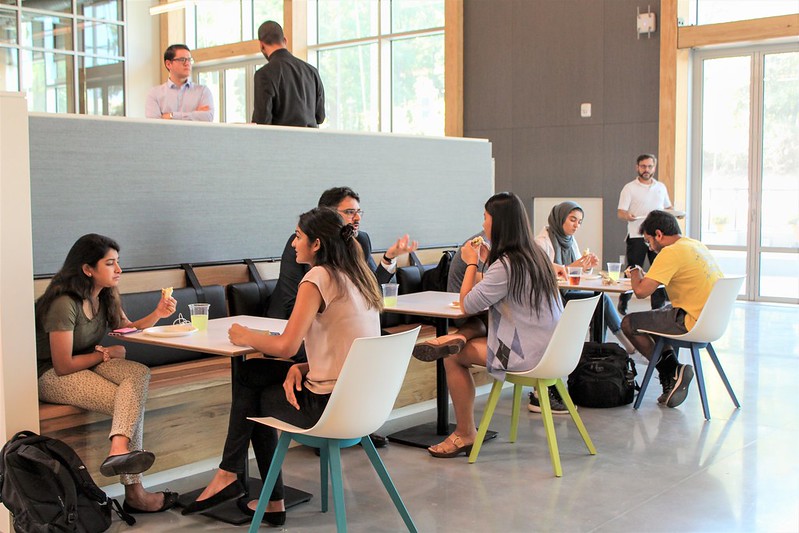
Reverberation Time Control
Red List Imperative
The Living Building Challenge includes a Red List Imperative specifying that all products used shall be noted as Red List Free or Red List Compliant, meaning the product does not include any of the chemicals on the Red List. The International Living Future Institute maintains the Declare label for products that lists all the product ingredients and other relevant requirements for sustainable designs. This is a search-able database of materials that are Red List Compliant.
At the beginning of the design phase the acoustical team searched the Declare database for Red List Compliant materials and found very few acoustical options, mostly limited to ceiling tiles. This prompted the team to reach out to a number of acoustical manufacturers asking about their products' ingredients and to investigate if their materials might be Red List compliant. The team additionally requested they consider submitting materials to the Declare database. While the options were limited for this project in design, we are pleased to find many of those manufacturers contacted did investigate further and today there are many material options and aesthetic choices for acoustical products in the Declare database.
Acoustical Absorptive Materials
The acoustical panels used for the project consisted of stretch fabric using the pvc free EcoTRACK track system, the Knauf Ecose Silent Fiber Line which is a phenol/formaldehyde-free mineral wool, and Red List compliant Maharam fabric. The panels were incorporated into the aesthetic designs to meet the interior design needs, installed between the windows allowing plenty of natural light, and leaving the wood ceilings exposed. Sufficient panels were incorporated to meet the ANSI S12.60 design goals.
The EcoTrack material was not commercially available at the beginning of the design phase. Through contacts with manufacturers' local representatives, we learned of the material and its planned market release closer to the start of construction. The material was available as estimated and submitted via Novawall for installation. The pvc free track is now available as an option from many of the major stretch fabric manufacturers.
Sound Isolation
The EcoBatt Unfaced Knauf Insulation was used for sound and thermal insulation at the interior and exterior walls. While more expensive, this Red List compliant mineral wool provides improved transmission loss, higher fire resistance, higher percentage of recycled glass, and is easier to install. The insulation met the acoustical needs and satisfied multiple aspects of the project.
HVAC System Noise Control
The HVAC system design started with energy and noise control in mind. The system relied on a decoupled concept using a dedicated outside air system for ventilation and dehumidification and radiant flooring systems for space cooling and heating. By using the radiant system, the amount of air delivered by the ventilation system is approximately 1/3 of that provided by a traditional system, which allowed the team to upsize the ductwork to reduce fan energy, which had the added benefit of reducing velocity and therefore breakout noise.
The main mechanical room is located in the basement, slab on grade, and far from the occupied spaces above. The dedicated outside air unit is located on the roof, but was strategically located over the building core to minimize noise and vibration transmission to program space. By scheduling maximum allowable sound power limits for the air handlers and terminal units, and working with the mechanical engineers on the duct layout and velocity, the ducted noise control design was limited to only 2 film-lined duct silencers.
Impact Isolation
The building structure was designed using wood from sustainably managed forests, salvaged materials, and even wood reclaimed from trees felled on the campus. This wood is featured throughout the building including in the exposed ceilings. The floors are a mixture of wood and polished concrete.
The radiant flooring system created an opportunity to incorporate impact isolation into the flooring design. Based on the project requirements, the Acoutimat 3 HP product by Maxxon was determined as the preferred solution to incorporate with the radiant flooring to provide impact isolation. Below is a photo of the radiant flooring installation over the impact isolation system and a detail showing the Acoustimat incorporated with the radiant flooring.
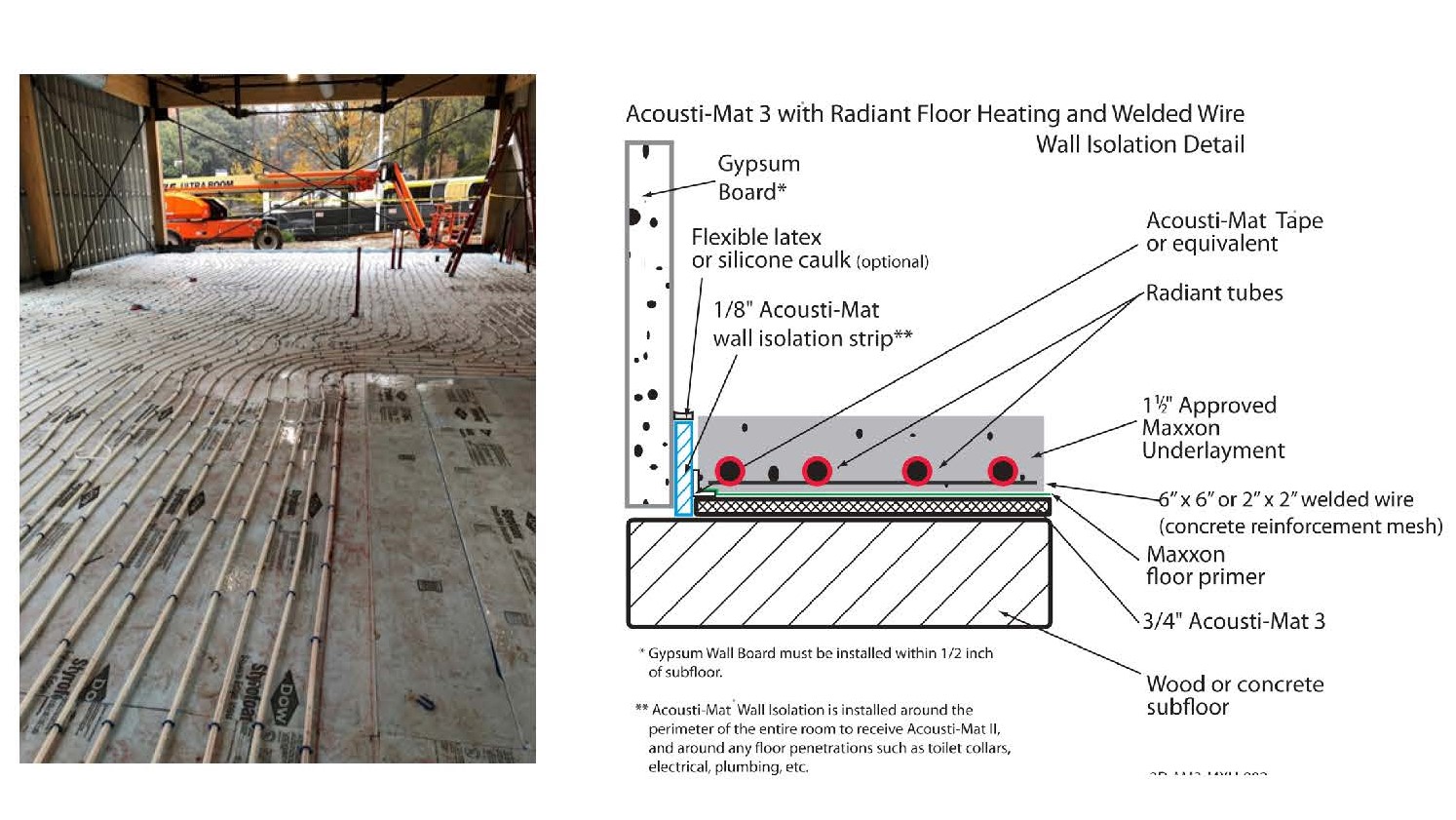
Exterior Noise Control
From the beginning of design, exterior noise was a concern because the Kendeda Building includes outdoor gathering, relaxing, studying, and farming spaces. The adjacent Krone Engineered Biosystems Building (EBB) and Marcus Nanotechonology Building (MNB) each has exterior mechanical equipment that was audible and objectionable at the Kendeda site prior to construction.
Measurements were taken at each building and the project site to determine the source of the noise and the most practical solution. Each of these buildings was in use and any mitigation solutions had to be balanced with research and class schedules to limit service impacts.
The EBB
The team walked the campus and determined the source of the tonal noise identified at the Kendeda site was coming from the ERUs on the roof of the EBB. Seven measurement locations were selected as shown below.
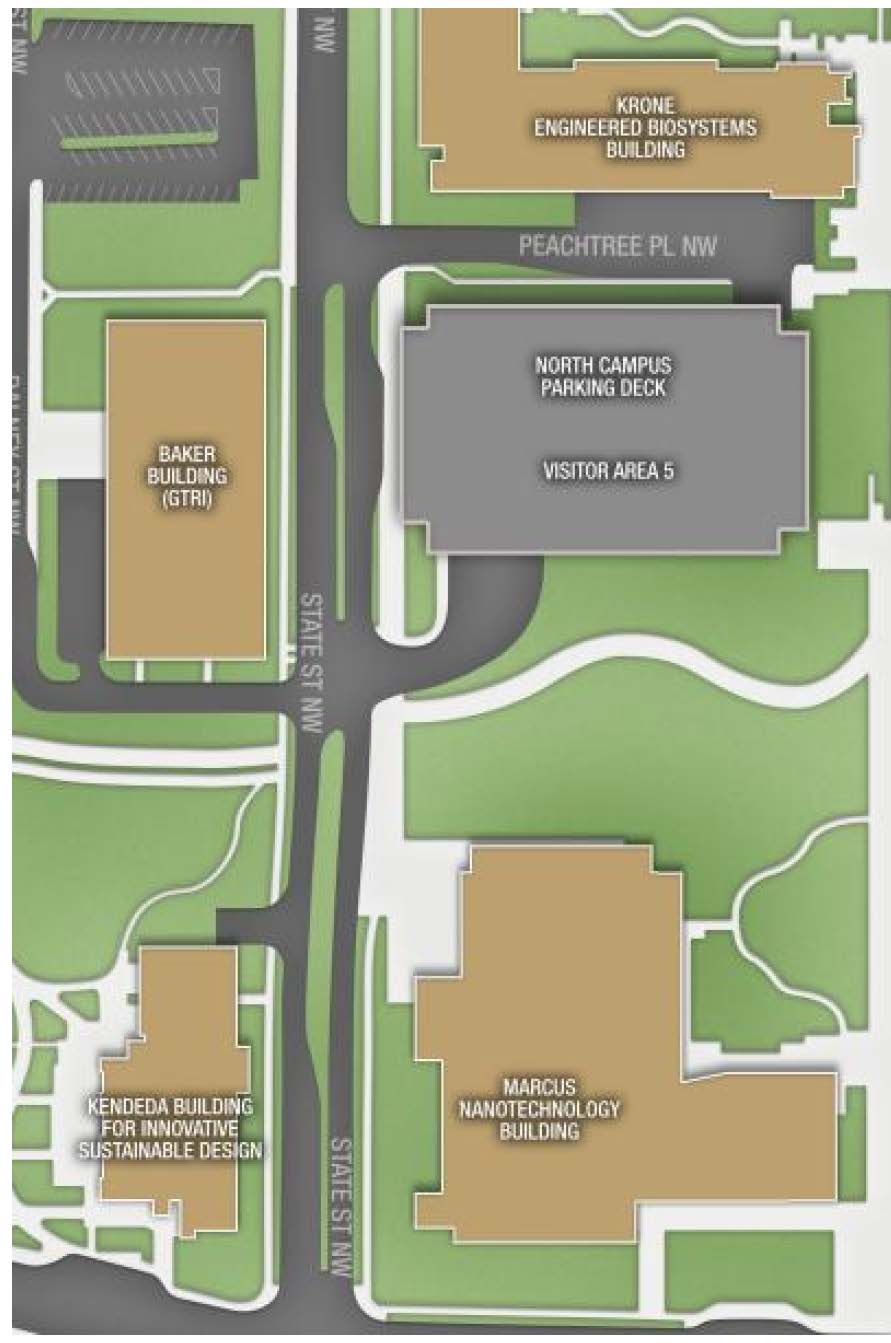
EBB equipment measurement locations attached for reference:
(text and background only visible when logged in)
Measurement locations at EBB and Kendeda Building attached for reference::
In addition to these 7 locations, 5 conditions were tested operating the the 3 ERUs at multiple fan speeds based on the building use cases. ERU-P01A was the unit exhibiting the tonal component at 400 Hz and 500 Hz depending on the fan speed.
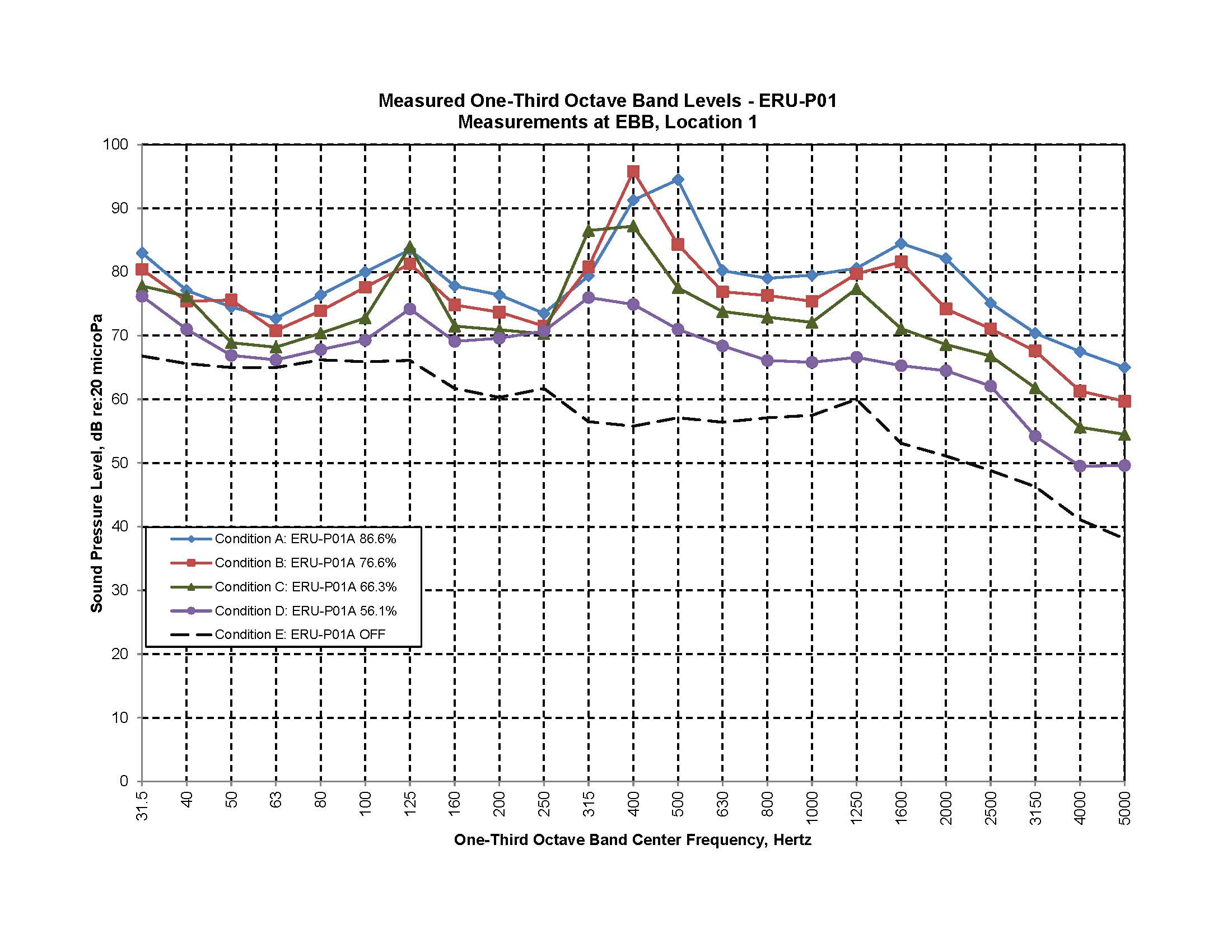
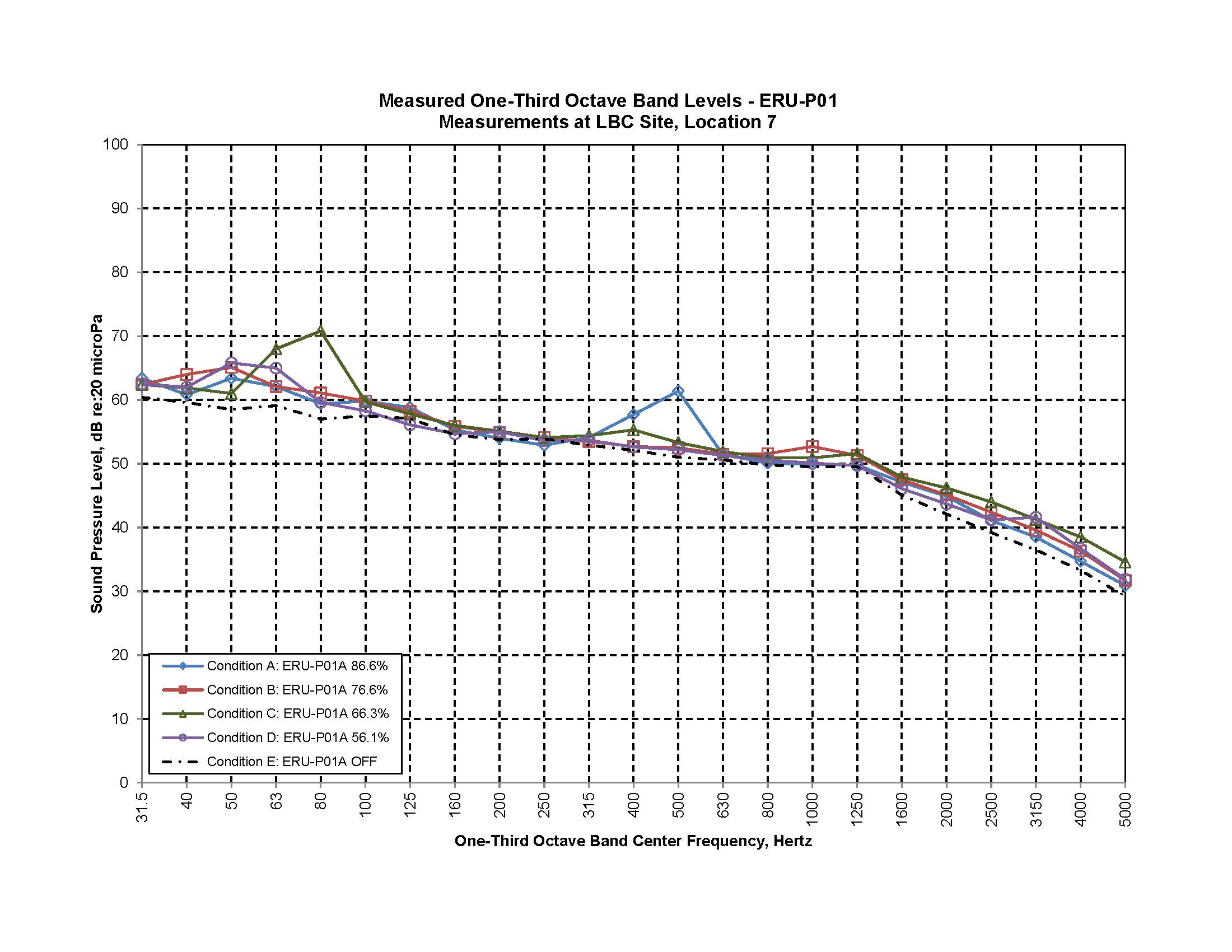
The 3 ERUs included additional capacity for future uses in the building. Therefore the most practical solution, chosen and implemented by the school, was to slow the fans on ERU-P01A. This eliminated the audible tone at the project site. Should future needs require the increase of the fans on the ERU, acoustical louvers were designed to mitigate the noise. The louvers were designed in conjunction with the mechanical team to limit the impact on the ERU performance.
The MNB
The Marcus Nanotechnology Building, located directly adjacent to the Kendeda site, includes lab exhaust fans (LEF), generators, exhaust fans for specific gases (Nitrogen and Silane), and chillers. Measurements were taken close to each unit and at the project site.
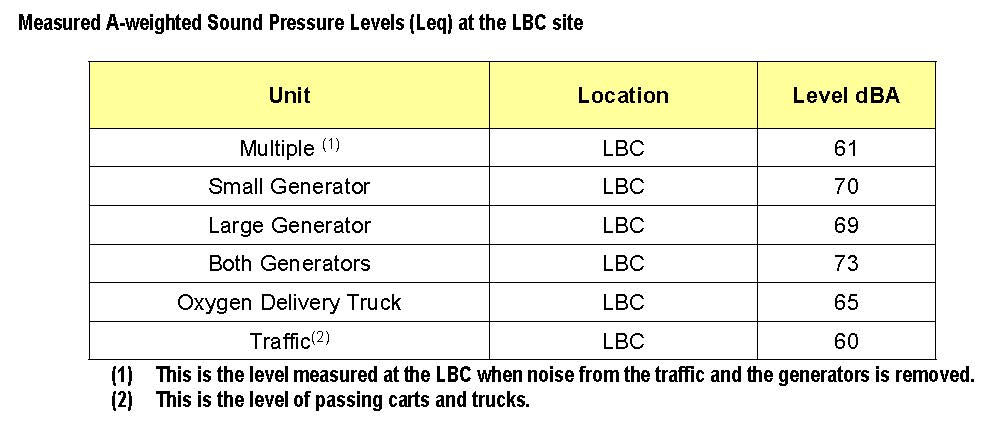
(text and background only visible when logged in)
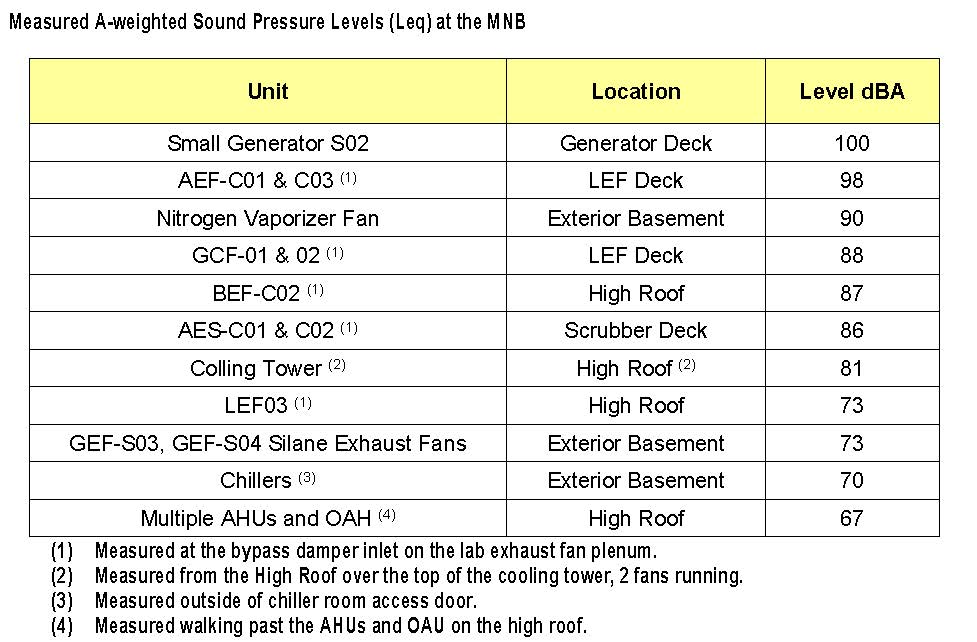
(text and background only visible when logged in)
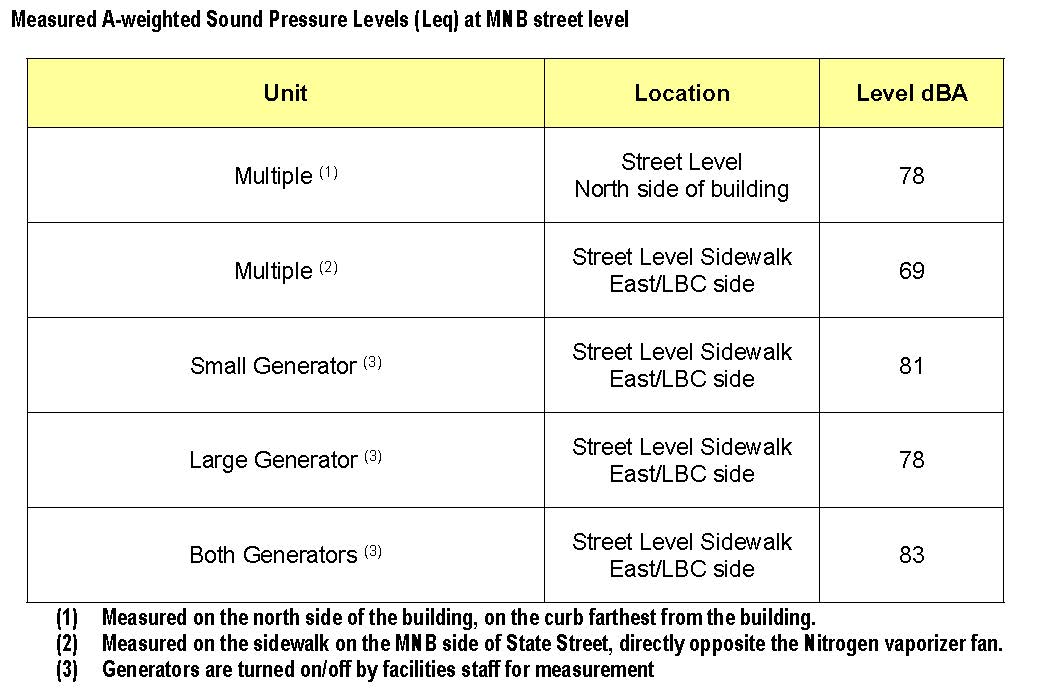
The highest impact was from the generators, followed by the lab exhaust fans and the nitrogen vaporizer fans. The team reviewed multiple options and chose those that provided the most improvement without impacting the building aesthetics, scheduled use, or functionality. The recommendations were provided in phases to allow for implementation with the school schedule. We understand that Phases 1 and 2 have been implemented and the resulting mitigation is satisfactory to the school.
Mitigation Options for Implementation
Phase 1 and Phase 2 were ways the Design Team outlined the mitigation options for implementation. There was also a Phase 3 that was not implemented. The Design Team “phased” them for cost and effectiveness and to match the school schedule for when things might need to be shut down for implementation.
Phase 1
- LEFs: Include by-pass inlet damper silencers, model FS-401-LF, on the LEFs located on the LEF and scrubber decks on the north side of the building. This includes but is not limited to HEF-C01, HEF-C02, HEF-C03, AEF-C01, AEF-C02, AEF-C03, GCF-C01, GCF-C02, AES-C01 and AES-C02. Bi-pass damper silencers are recommended even on the future expansion locations as each damper opens into the same air plenum.
- Generators – assuming generators are only for emergency use and weekly tests, schedule generator test runs for times of lower campus occupancy perhaps before 8am classes.
- Nitrogen Evaporator Fans – review options for quieter operation. Replace with quieter fan option including vibration isolation or replace with a fan-less system.
- Chillers – Review thermal seals on roll doors and single-width door. Replace seals that are showing wear and add seals if missing. Confirm door is sealing well and closing completely.
Phase 2
- LEFs: Include by-pass inlet damper silencers on the remaining LEFs.
- Silane Fans S04 and S05 basement level: Wrap fans with mass loaded vinyl over quilted fiberglass blanket. Use a product such as Insultech by Shannon Enterprises.
DATE PUBLISHED: May 10, 2022
AUTHOR: Jessica Clements
ORGANIZATION: Newcomb & Boyd, LLP
PROJECT ROLE: Acoustical Consultant
TELEPHONE NUMBER: 404-730-8429
EMAIL ADDRESS: jclements@newcomb-boyd.com